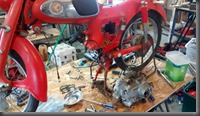
One of the things I enjoy about working on old bikes is that you can (and often have to) do the work the low tech way.

Having free labour and not being under the gun to meet performance targets means you can do things differently. As an example, the shifter shaft on the S65 was bent. A replacement is readily available but I have a friend with a hydraulic press, so instead of simply ordering a new part we spent 1/2 hour or so gently bending the shaft back into alignment. If I was a shop owner there’s no way I’d allow my technicians to be “wasting time” doing that – put in a new part and be done with it. As a consumer paying $100 an hour to the shop I’d probably agree. And when parts just aren’t available, repairing what you have is the only option.


Likewise with tools. Every motorcycle shop manual I own has a section in the back listing all the special tools needed to work on that particular make and model. But with some ingenuity and time it’s pretty easy to either make do or fabricate something that will work just as well. One of the more common special tools is a socket to remove a notched clutch locknut. I don’t have one but I did have a piece of 1” black pipe and a file. Voila – special tool! And it worked a charm. (I have a similar tool for a 1974 Kawasaki Z-1 that I’m hanging on to “just in case”.) To remove the valve springs a C-clamp and a home-made spacer did the trick.
I’m sure there’ll be lots more opportunities to be creative and improvise but one in particular will be when I jury rig something to take a slight twist out of the stamped steel frame. My friend with the press was in the body shop business many years ago and describes straightening bent auto frames with one end chained to a tree and the other to a tractor – then eyeballing when it got “close enough”.
I probably won’t need the tractor, but chaining one end to a tree might give me the leverage I need. Stay tuned for that experience.
Fascinating! That old adage, "Necessity is the mother of invention" certainly hold true in your shop, Dave
ReplyDeleteAnd "being cheap" is the father of invention. :)
DeleteHmm, that looks like an early Mustsng tied to the tree. Nice tool fabrication. I'm finding that the one more "needed" tool is a welder. Just think how easy that tool would've been to make if you had an end mill...
ReplyDeleteRichard - Have the welder, but an end mill - only in my dreams.
DeleteYou nailed it! The goal is the repair but the fun part is how you go about the repair.
ReplyDeleteIt's not the destination but the journey.
DeleteThe question I have is how did that part get bent to begin with? Any ideas?
ReplyDeleteI think the engine took a good blow on the left side, bending the shaft and cracking he case where it seats. The case had been repaired (sort of) but for some reason the owner at the time didn't think the shaft should be straightened. Or more likely decided the hell with it and just buttoned it all back up and sold it.
DeleteMy hubby swears by this type of do it yourself tool making. We have found plenty of uses for the 2x4 he keeps for helping to bend things back and uses as a wedge.
ReplyDeleteAh yes, the ubiquitous 2x4 - nature's lever, mallet, wedge, drift, and general go-to tool when something needs a good non-marring whack.
Delete